Requirements for FRP Sluice Wells
Introduction: FRP septic tanks are made of synthetic resin as the matrix and glass fiber reinforced materials and are specially designed for the treatment of domestic sewage. The glass fiber reinforced plastic septic tanks are widely used for their advantages of high strength, good toughness, and corrosion resistance. In the chemical, petroleum, construction, textile, aviation, electricity, metallurgy, machinery, environmental protection and other fields.
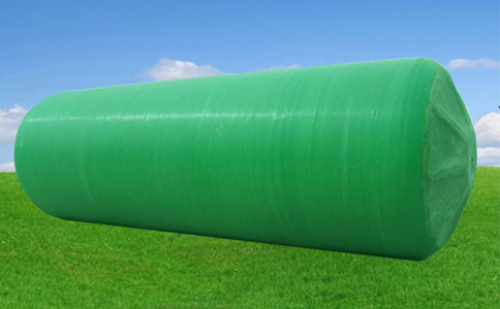
The glass fiber reinforced plastic septic tank is made of synthetic resin as the matrix and glass fiber reinforced material. It is specially used for the treatment of domestic sewage. The glass fiber reinforced plastic septic tank is widely used in chemical industry due to its advantages of high strength, good toughness, and corrosion resistance. , petroleum, construction, textile, aviation, electricity, metallurgy, machinery, environmental protection and other fields.
Construction process of glass steel septic tank cleaning wells
1. Backfill to meet the requirements of the construction specification. The well body can be built with clear wells (inspection wells). There are two kinds of brick wells and group prefabricated reinforced concrete wells.
2. Inspection wells In order to prevent the leakage of the brick wall, the inner and outer walls of the well shall be waterproofed with a mortar and plastering layer. The thickness shall be 20mm (1:2 waterproof mortar, 5% of the water resistance of the internal reference cement weight), and the inside corner shall be wiped. 45. Beveled, 50mm thick. When groundwater is present, apply hot asphalt (or other waterproof coating) on ​​the outside of the well. Finally, cover the soil to the floor.
Requirements for the construction of a glass reinforced plastic septic tank for clearing wells 1. When excavating the foundation tank, the geological conditions should be mastered.
2. The location and buried depth of glass steel septic tanks should be laid and positioned strictly in accordance with the design requirements.
3. After the glass fiber reinforced plastic septic tank is in place, backfill the soil in time and fill the tank with water to prevent displacement. The backfill requires sifting. There is no sharp corner stone and construction waste. When there is no groundwater, the soil density is 0.95 compacted. Special attention should be paid to the use of plain soil or yellow sand around the tank body: when there is groundwater, the tank body should be filled with plain soil or yellow sand, and the tank body should be evenly loaded.
4. During the construction of the rainy season, drainage facilities shall be provided to prevent water accumulation in the foundation pit and collapse of the slope. At the same time, the tank body shall be filled with water to prevent it from floating and cause displacement.
5. Construction shall comply with the provisions of the relevant project construction and acceptance specifications.
Process:
The foil roll is introduced into the rubber roller of the feeding device via the decoiling machine and then would in the winding former after passing through the edge of the shearing machine and the roller wheel of the burr pressing device. The inter layer insulation coil is erected in the rear of the coiling optical shaft of the foil winding machine and wound in the winding former after sheared by the trimming roll and the shears blade.
Functional feature:
1. The device adopts and electrical servo deflection correction system to achieve manual/automatic adjustment of the foil position more conveniently and reliably.
2. An advanced electrical control technology of constant tension is adopted to control the tension of the foil and the inter layer insulation, with the features such as quantitive, accurate and convenient control of the tension no mechanical friction. The required tension can be maintained for forward winding, stop and backward winding, ensuring compact coils.
3. The inter layer insulation adopts a cantilever mechanism, convenient for feeding and the mechanism can be pulled out as a whole without guide rails outside the body.
4. Automatic welding mechanism and roll shearing mechanism adopt ball screws and linear guide rails for drive, ensuring the service life and accuracy of the device.
5. This device first adopts the all-in-one sing frame, solving problems such as few coil urns and deflection correction lag.
6. This device is a hi-tech product produced by combining with actual production on the basis of many similar products at home and abroad. The whole machine is controlled via an advanced PLC touch screen, with high automation level and simple and reliable operation, representing higher production level of domestic foil winding machines.
Cnc Winding Machine,Foil Winding Machine,Cnc Wire Winding Machine,Hv Foil Winding Machine
JINAN EURO-ASIA MACHINERY CO., LTD , https://www.eaelectricmachine.com