"Core" was created to unveil Xiechai's "three lead" veil
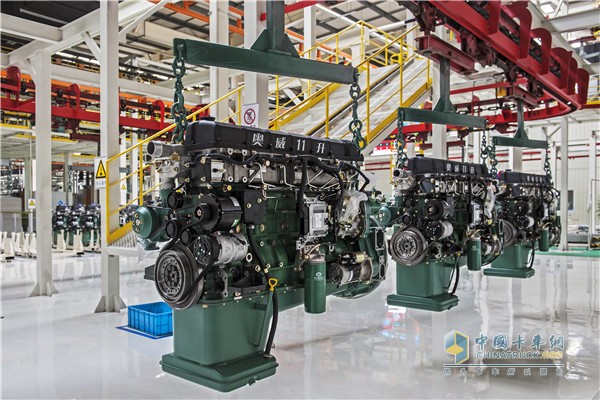
In this area of ​​254,200 square meters, with a total investment of 2.2 billion yuan in the production base of heavy-duty diesel engine, you will not only be reflected in this "green, digital, lean", and "leading design, equipment leadership, Leading the "leading three" engine production base is shocked, but will also be XiChai employees in this piece of hot land carefully created national brands, high-end power of the tenacity.
Design Leading Smart Manufacturing Industry
"Design leadership is first embodied in green, high-efficiency, and intelligence." Walking on clean production sites, the base leaders are delighted to say that this is the first domestic use of ground source heat pump technology, cold test school bus technology, alternating current power dynamometer technology, and the use of natural gas Heating and drying, solar water, and domestic water equipment have achieved low carbon emissions from production. Its comprehensive use of advanced concentrated cutting fluid for the last time, closed processing and suction fog and other technologies, the production site will never appear ground oil, dust pollution, but also reduces the emission of pollutants to the atmosphere, to achieve a beautiful Production Environment.
“Xichai's heavy-duty vehicle engine intelligent manufacturing pilot demonstration project is a shortlist for the 2016 National Smart Manufacturing Pilot Demonstration Project, which will have an important significance for promoting the transformation and upgrading of the entire internal combustion engine industry. According to the leadership of the base, the four The intelligentization of the machining production line and three assembly lines has given Xicva Aowei machines an excellent genetic code. The mechanical processing line adopts the design concept of single unit and unit group in series and parallel integration, which fully utilizes the advantages of various wiring modes and improves the production efficiency. The assembly line adopts a "one-stream" production model to realize the efficient production and logistics organization. It is reported that the full use of digital design technology in the construction of the base, the use of three-dimensional modeling, production line simulation, simulation and other methods to ensure that the design goals to achieve and optimize investment. A large number of automated intelligent equipments are used, integrating automation, flexibility, integration, and intelligence to improve production efficiency, improve quality assurance capabilities, and reduce manufacturing costs. Full use of modern IoT technology to achieve automatic collection of manufacturing data and equipment Monitoring, quality analysis; application of big data analysis technology, to achieve a highly efficient and intelligent manufacturing system.
Approaching the assembly line, the cold test stand with silvery white luster is particularly eye-catching. At this time, the 11-liter aowei heavy-duty electronically-controlled common-rail diesel engine on the assembly line was slowly moving toward the cold test bench. Within a few minutes, a clean Aowei heavy-duty diesel engine was cold-tested. The plugs and clamping units at the stations are returned and released. All the data tested at the factory are “in one go†on the computer operation screen. The entire process is environmentally friendly and efficient. According to the leaders of the base, Xichai is the first domestic heavy-duty diesel engine manufacturer to use the data. The manufacturers of engine cold test technology, compared to the traditional hot test technology, the adoption of this technology makes the school bus no longer consumes diesel fuel, does not need a large amount of water, electricity, gas supply, and will not have exhaust emissions, truly low Carbon environmental protection green production.
FAW Xichai production line
Even more gratifying is the recently concluded 2016 China Machinery Industry Science and Technology Awards, FAW Xichai's "Heavy Duty Diesel Engine Advanced Manufacturing Technology Research and Industrialization" project and "CA6DM Heavy Duty Diesel Engine Cold Test Process Study and Batch Application " Both projects won the second prize.
Equipment Leading Achievement Aowei High-end Quality
In the market, the key is quality, and the key to quality assurance lies in the leading edge of equipment.
The Aowei series of engines such as the CA6DM2, CA6DM3, and CA6DL3 manufactured by FAW Xichai Huishan heavy-duty diesel engine production base are outstanding representatives of Xichai's "high-end power". Among them, the CA6DM 11-liter engine won the first prize for national science and technology progress. The diesel engine adopts advanced technologies such as four-valve, double-decker cylinder head, overhead camshaft, high-pressure common rail, exhaust brake, etc. It has wide power coverage, large torque, low product oil consumption, and high emission levels. Salient features.
"The 6DM cylinder block production line here is GROB's first heavy-duty diesel engine block production line in the world." The leader of the base proudly stated that equipment leadership is an important factor in ensuring the high quality of Aowei 6DM machines. The whole line of equipment here is processed and assembled. Transportation, testing, school buses, etc. are all provided by leading international equipment suppliers. Among them, the 6DM 11-liter engine assembly line adopts NC control to realize automated operation with robots, power manipulators, truss manipulators, and EMS systems. At the same time, the entire line design adopts various error-proof technologies such as visual error prevention, laser error prevention, and mechanical error prevention. , To achieve a 6DM11 liters of diesel engine efficient production and product quality.
In the 6DM coating line, two Swedish ABB robots are facing the orderly automatic spraying of the whole machine. The base staff said, “The 6DM11 litre engine paint uses the paint transfer system to reduce the manual paint adjustment and ensure the paint quality. The use of water spin-type paint spray booths, paint mist treatment efficiency, three waste treatment technology leading domestic.
FAW Xichai Painting Workshop
"In order to ensure that Aowei CA6DM engine cleanliness testing standards lead the industry, the base has also formulated cleanliness improvement measures and rules from self-made parts, logistics distribution, assembly and other dimensions, ensuring that the cleanliness of 6DM machines has reached the domestic leading level. It is understood that in order to ensure the quality of Aoweigao, the base production line not only uses a number of error-proof technologies such as laser error prevention, photo error prevention, quality information collection central processing system, etc., but also monitors through monitoring stations and detects key dimensions on Marposs Online. Instrument to test to meet the quality indicators. At the same time, it also uses standard operating instructions, error prevention techniques, and process control (SPC) quality control systems. With advanced quality concepts, stringent quality standards, and scientific quality assurance methods, the high-end quality of Xichai is ensured.
At present, professionally benchmarking the CA6DM 11-liter engine produced by this company and the world brand's same-emission product, the benchmark results show that the overall performance is comparable, and that the xikai machine is also slightly superior in terms of fuel consumption; in terms of product reliability, The latest reliability index -12MIS failure rate has reached the international advanced level; in the product durability, the B10 engine life of Xichai far exceeds the competition.
Management leader engraved efficient and proud
Today, the Aowei CA6DM 11-liter engine produced by the base has become a golden symbol for liberation, leading the trend of heavy-duty engines, making the liberation of 460-horsepower heavy trucks the fastest growing market this year, and also making 100,000-kilometer-long oil changes become the industry's Benchmarking, let the base from the beginning of 2016 began to enter the high yield period every second.
“The daily production capacity of M machines hit a record high. From January to December of 2016, the output of 6DM cylinder blocks, cylinder head self-manufactured parts and 6DM assembled diesel engines respectively increased by 82.5%, 78.05% and 90.21%.†It is reported that the base is centered around the total efficiency. The organization established and evaluated the LTE lean production index evaluation method to ensure high productivity and efficiency. They have shifted from focusing on various processes and influencing factors of the production organization process to focusing on the whole factor of restricting total efficiency; from setting up multi-dimensional and decentralized processes and outcome indicator groups, to setting up a systematic system with overall efficiency as the core Indicators change. The base uses scientifically quantified settings to use production efficiency evaluation indicators as a means of organizing each team to accurately identify major issues. Through integrated dispatching and utilization of resources, major problems are solved, and LTE (production line total efficiency) is continuously improved. As of December 2016, machine-added lines and assembly line LTE reached 91% and 92%, respectively, leading the industry in production line efficiency, shortening the production cycle by one hour, increasing labor productivity per capita by 10%, and setting a single-month Aowei CA6DM 11-liter engine. The output exceeded the historical record of 9,700 units.
“Innovation management model, improving leanness and maturity, establishing a benchmark for self-determination.†In 2016, the base innovated new ideas for FPS “Effective, Convergence and Innovation†in the departmental department, organized the department's FPS promotion framework and implemented it, and was listed by the group as an independent system benchmark. . Their innovative new lean production efficiency evaluation system focuses on improving the overall efficiency of the production line, scientifically quantifying production efficiency evaluation indicators and using them as a means to achieve accurate identification and resolution of major problems, and reducing and eliminating various wastes in the manufacturing process. The goal is to continuously improve and improve the lean production evaluation system for production capacity.
In order to increase production efficiency, the base also focuses on preventing the implementation of equipment maintenance this year, optimizing the management of post-failure evaluation of equipment, analyzing the equipment failures that affect bottleneck process efficiency, analyzing the two dimensions of failures no longer occurring and improving maintenance efficiency, and comparing the same equipment. In other words, the components were inferred from each other, targeted preventive maintenance was implemented, and the rate of equipment shutdown was reduced. From January to December of 2016, the equipment could always be maintained at more than 99.5%, which effectively ensured the smooth progress of high output.
The essence of management is not "knowing" but "being". Its verification is not in logic but in achievement. In terms of factory management, the base has been designed through scientific and advanced processes, and modular modular talents have been developed. The 6DM assembly line has won the highest honor of the "five-star site" in the nationwide spot management star rating activity organized by the National Quality Association.
FantasView Multi-Fit Plastic Rear Wiper Blades:
- Have 4 adaptors cover 95% Rear Wiper Applications
- 4 New SKU=16 Old SKU
- Available Size: 11" 12" 14" 16"
- MOQ: 0nly 100pcs/each size
- Fit for most of American Cars, European Cars, Japanese Cars, Korean Cars
- Easy Installation, and good performance
- Competitive Prices
Multi-Fit Plastic Rear Wiper Blades
Multi-Fit Plastic Rear Wiper Blades,Multi-Fit Plastic Wiper Blades,Plastic Wiper Blades,Multi-Fit Windshield Wiper Blades
NINGBO FANTASVIEW WIPER BLADES CO., LTD. , http://www.fantasview.com