Fire Furnace Flame Detection System Commissioning in Xiangfan Power Plant
The Xiangfan Power Plant boiler is a subcritical intermediate reheat natural circulation drum boiler produced by Shanghai Boiler Works. The burners are arranged in a four-corner arrangement with cut-out combustion, and four sets of CW-type wide-range control ratios (WR burners) are arranged in the lower corners of the furnace. Each burner consists of 5 layers of primary air nozzles, 8 layers of secondary air nozzles and 2 layers of tertiary air nozzles. Among them, 3 layers of secondary air nozzles are equipped with light oil guns. Each oil gun is equipped with a corresponding High-energy igniters, automatic control ignition, oil guns using the mechanism of atomization, burner coal powder nozzles and oil guns are equipped with flame detection devices.
First, the system composition and detection principle Xiangfan Power Plant flame detection device is provided by the United States FOR-NEY company, its main components include the two major parts of the detector and amplifier. The detector part consists of a probe and fiber optic cable components.
1. Fiber optic cable components: provided by the United States Fireye company, which consists of optical lenses, fiber optic bundles and internal and external stents and other parts. Optical lenses are mounted near the boiler's bellows and furnace walls. The inner bracket is connected to the outer bracket through a metal hose from the furnace wall of the boiler. Internal and external stents are mainly used for fixation. The bundle is placed in a metal hose and the fiber is connected to the probe.
When the burner oscillates, the ventilation system in the bellows, or the nozzle of the burner affects the viewing angle of the flame probe to the furnace flame detection, we need to draw the flame out through the optical fiber. When a conventional boiler is burning, a large fireball is formed in the furnace. In conventional tests, the flame of a single burner is used to determine the presence or absence of a burner flame. In order to avoid the impact of the fireball on the individual burner flames and facilitate the accurate measurement of the individual burner flame states, some adjustments have to be made to the flame measurement angle, and the use of fiber optic cables is precisely to satisfy this requirement, which can be achieved more easily The installation increases the accuracy of the measurement. At the same time, the probe can be kept away from the high temperature zone of the boiler through the optical fiber, which advantageously protects the components of the probe.
2. Probe: Model DPD (IR) is smart. Mainly the flame burner combustion shape stored in the text, the use of microprocessors and software calculations, continuous measurement of the flame amplitude and frequency characteristics to determine the state of the flame, and the flame combustion conditions into pulse signals.
Each burner has its own specific flame shape, including its shape (envelope) and flame strength. The DPD probe thus forms a text. In the learning (Learn) mode, the frequency characteristics of the target flame signal are analyzed in real time, and the flame type (for example, flame, adjacent flame, background flame, no flame, etc.) is determined. Flame spectral characteristics image. In the "RUN" mode, the measured flame signal can be compared and identified with the archived flame to determine the state of the flame.
This digital text technology design greatly simplifies the man-machine interface and simplifies the static verification of the probe. In particular, self-diagnosis and "step-by-step" programming make the probe easy to operate.
3. Flame amplifier: Its model is DP7000, receives the flame pulse signal that the probe sends, and carries on the comprehensive processing, sends out the existence/no flame state signal, the critical flame warning signal and the 4-20mA flame signal.
Second, the installation quality of the furnace flame system of the system will directly affect the measurement results of the flame detection device, especially the detector part, which is an important part of the process of converting the flame signal into a processable digital signal. It is a primary component of the system and is Boiler furnace in front of the place. The following briefly describes several issues that the detector section should pay attention to during installation:
1. The center line of the inner frame of the detector and the flame center line of the burner should be at an angle of about 5 degrees to ensure that the detector is aligned with the initial combustion zone of the flame.
2. The detector's fiber bundle hose section should try to bypass obstructions (such as air baffles, etc.), or open holes (slots) in place on obstacles. Trial air baffles before the trial run to check whether the hose or bracket collided, taking into account the expansion of the boiler stroke.
3. Install the detector should pay attention to the direction of rotation of the furnace secondary air, the detector should be installed in the direction of rotation of the gas flow igniter 10-30 degrees.
4. The location where the detector is installed should work in the visible target area of ​​50-150cm. If the viewing area is too large or too small, it is easy to cause "peeping phenomenon" or "flame distortion".
5. Probes should be free from contamination with oil, ash, smoke, and other contaminants. The temperature of the probe mounting position must not exceed 65 °C, otherwise it will affect the life of the probe.
6. The probe must be insulated from ground. Insulation cover should be installed on the bracket. The insulating sleeve has two functions. One is to prevent heat conduction, to prevent the heat of the furnace from being conducted to the probe along the bracket, and the second is to electrically insulate to avoid interference with the measurement signal and noise. The measurement signal connection should be shielded and connected to the DCS grounding system to prevent strong electrical interference.
Third, the system's debugging and maintenance The flame system's debugging is to make the system correctly reflect the fire mouth combustion conditions, accurately identify the burning of coal or fuel, and will not peep into the upper and lower or adjacent fire mouth and the entire furnace background flame. In the debugging process, the Forney intelligent flame probe is first set statically and dynamically adjusted to adjust the flame combustion conditions. Static tuning of the probe involves configuring the probe to generate a text, then storing the text and putting it into operation. A complete text contains a set of parameters and existing flame presence/absence files. There are eight LED displays on the probe and four buttons for setting different values ​​and parameters. Three of the buttons are on the probe surface. They are Advance, Help, and Change.
Advance: Displays the file content and directory.
Help: Explain the meaning of the contents of the file.
Change: Modify the setting value in the range of the directory. Press the programming enable button before changing the number.
On the side of the probe (inside the housing) there is the Program Enable key, which is the programming enable key for programming permission.
The main steps of programming are as follows:
1. Press the Programming Enable button to set the probe in the set state.
2. Programming file text.
3. Configure the status and various parameters of the probe.
4. Adjust the angle, range and sensitivity of the probe to the flame. Learn to have a state of flame.
6. Learn the flame without state.
7. Store text data.
8. Put the probe in operation for use.
The detectors have two levels of lists, ie status lists and setpoint programming lists. The status list is only used to display the status information of the detected burner flame of the current detector. The set value list is used for static and parameter setting of the detector. Refer to Table 1 and Table 2 for the specific setting adjustment.
The dynamic debugging of the detector is to learn the flame of each burner separately under a certain load condition. During the dynamic debugging process, the boiler load must be kept stable (cannot swing the fire nozzle), and the combustion conditions of the adjacent fire nozzles must remain unchanged. The detector screen shows that LRN=110 starts decrementing, when it is reduced to 100, NEWDATA is displayed, and then continue. During the learning process, if there is a change in load or the removal or input of an adjacent flame, the display will show NEWDATA again and reset to 100. The count will be restarted. When it is reduced to 0, the learning is completed. Specific debugging is as follows:
1. When the unit is under high load (above 270MW or above 90% load), the coal fire inspection is performed at the feed mill speed of 400 rev/min and 700 rpm, respectively, with the fire (burner put into operation) and without The LearnOnNew and LearnOnAdd settings are performed separately under fire conditions (burner removal) and then put into protection.
2. After the above adjustments, the unit reduced loads to 240MW (80% load) and 200MW (70% load) stable conditions, check the actual operation of the flame and perform burner injection/cutting experiments to check if it is true and whether there is any false flame.
3. In order to ensure that the fire detection can work stably under any conditions, the boiler load should be reduced to about 170 MW (without fuel injection), and then the coal fire should be checked one by one at a feed rate of 400 rpm for the LearnOnNew setting. , and then carry out LearnOnAdd adjustment at a high speed of around 700rpm.
4. If there is instability in the fire detection during operation, it can be used for 1-2 times to increase or decrease the load. Follow the above steps to perform LearnOnAdd adjustment.
Second, configure and debug the fire detector amplifier. Each DP7000 amplifier can receive the pulse signal sent by two fire detection detectors. Xiangfan Power Plant adopts one-way configuration. The amplifier's display values ​​are also divided into two groups, the status group and the setpoint configuration group. The status group shows the operating parameters. All parameters are displayed in abbreviated form. See Table 3:
The setpoint configuration group is used to configure and modify the amplifier. In the process of dynamic debugging fire detection and determination of the relay action value according to the actual situation. We set about 200pps. In the actual debugging process, we usually have a firing frequency of about 250pps. The operating value of the sending signal relay should generally be 50 pulses lower than the measured value, and the non-fire frequency is about 150pps. The critical alarm flame action value is less than The fire action value is 20 pulses high. See Table 4
Through the debugging of the probe and amplifier, it can be seen that there is a fire response time of 1 second, and the total time for the flame to lose response is 4+1=5 seconds. That is, no flame is observed from the probe until the amplifier emits no flame signal for 5 seconds.
Fourth, factors that affect the flame detection and analysis of the type of boiler combustion The type of fuel on the boiler combustion equipment structure selection, boiler layout and boiler safety and economy have a greater impact, a direct impact on the boiler's combustion, and combustion status The stability and flame shape of the combustion also affect the accuracy and sensitivity of the flame detection. The following sections explain these aspects separately:
1. Effect of Burning Mode on Fire Detection Forney's fire inspection system forms a text with flame shape and flame intensity. Based on this, the text is analyzed and processed through specific software. Different combustion methods form different background flame shapes, which have different effects on the burner flame. Therefore, the processing of the flame signal in software is not universal. At the same time, the upper and lower flames or adjacent burners The influence of flame is different, and the discrimination of flame detection by digital text has a great influence.
2. The influence of combustion on the fire detection The stability of the combustion dynamic process is of great significance to the measurement of the flame. Although the stability of the combustion is directly related to the fineness of the fuel and the fuel/wind ratio, it is also closely related to the type of fuel. Inseparable. From the conventional analysis of fuels, when the coal is burned, except for a part of the fixed and free hydrogen, the elemental composition is not a single-state combustion, but a complex organic combustion is involved, and the combustion process is roughly the same as the analytical process in industrial analysis. Therefore, the factors that directly affect the combustion and operation of the boiler are mainly the industrial analysis components of coal, namely volatile matter, moisture and ash. Now briefly describe their effects on combustion:
(1) The effect of volatiles The more volatile the coal, the easier it is to ignite and the combustion is easy to complete. This is because: the volatile matter is a gas combustible material, the ignition temperature is lower, the more volatiles, the lower the ignition temperature, so that the coal is easy to catch fire; more volatile matter, relatively less than the coke fired in coal; Volatilization analysis shows that burning can release a large amount of heat, causing high temperature in the furnace, which helps the rapid ignition and combustion of coke. Therefore, the volatile coal is also more prone to burnout. The volatiles are precipitated from the solid fuel and precipitated. To make the fuel porous, the more volatiles, the greater the porosity of the fuel particles, the greater the contact surface between the fuel and air, to facilitate complete combustion. The design coal of Xiangfan Power Plant is 50% mixed for Dengfeng lean coal and Huangling bituminous coal. The flammable radical is divided into 22.62%, and the checked coal A is Henan Dengfeng lean coal with a volatile content of 14.22%. The checked coal type B is Shaanxi Huangling bituminous coal with a volatile content of 35.46%. The large-scale changes have a great influence on the detection of the fire detection system. When the coal type changes, dynamic learning adjustments are needed.
(2) The effect of moisture The amount of water in the coal is high, the effective heat released when burning is reduced, and the amount of water is high, which reduces the combustion temperature in the furnace and increases the heat of ignition. This can delay the fire and even make it difficult to catch fire.
(3) Effect of ash Not only does the ash content in the fuel not burn, but it also reduces the amount of heat generated by the fuel, hinders the correct connection between the flammable substance and oxygen, increases the difficulty of ignition and combustion of the fuel, and also increases the combustion loss. An increase in the ash content of the fuel can slow the flame propagation speed, affect the ignition, and reduce the flame temperature, because the heat consumption of the heated ash increases. The lower calorific value of coal, the greater the ash content and moisture content, the greater the temperature drop caused by the increase of ash content.
V. Conclusion Forney's intelligent flame detection system analyzes and processes the flame state through text processing, providing us with a new set of measurement methods. Based on microprocessor and software calculation and analysis, the strength (magnitude) and frequency characteristics of the flame under test are constantly inspected, and the static setting of the system and the verification of the measurement components are conveniently achieved, simplifying the man-machine operation and providing a flame detection device. The development and application have opened up new directions. However, in actual operation, changes in operating conditions or changes in coal quality have a greater impact on the accuracy and sensitivity of the measurement, and even result in erroneous results. It is necessary to continuously adjust the learning process according to the actual situation. The staff has increased the workload, and at the same time it has strict requirements on the stable working conditions in the adjustment process, and it can only be determined by raising or lowering the load several times, which increases the difficulty for the operating personnel and also increases the production and operating costs.
First, the system composition and detection principle Xiangfan Power Plant flame detection device is provided by the United States FOR-NEY company, its main components include the two major parts of the detector and amplifier. The detector part consists of a probe and fiber optic cable components.
1. Fiber optic cable components: provided by the United States Fireye company, which consists of optical lenses, fiber optic bundles and internal and external stents and other parts. Optical lenses are mounted near the boiler's bellows and furnace walls. The inner bracket is connected to the outer bracket through a metal hose from the furnace wall of the boiler. Internal and external stents are mainly used for fixation. The bundle is placed in a metal hose and the fiber is connected to the probe.
When the burner oscillates, the ventilation system in the bellows, or the nozzle of the burner affects the viewing angle of the flame probe to the furnace flame detection, we need to draw the flame out through the optical fiber. When a conventional boiler is burning, a large fireball is formed in the furnace. In conventional tests, the flame of a single burner is used to determine the presence or absence of a burner flame. In order to avoid the impact of the fireball on the individual burner flames and facilitate the accurate measurement of the individual burner flame states, some adjustments have to be made to the flame measurement angle, and the use of fiber optic cables is precisely to satisfy this requirement, which can be achieved more easily The installation increases the accuracy of the measurement. At the same time, the probe can be kept away from the high temperature zone of the boiler through the optical fiber, which advantageously protects the components of the probe.
2. Probe: Model DPD (IR) is smart. Mainly the flame burner combustion shape stored in the text, the use of microprocessors and software calculations, continuous measurement of the flame amplitude and frequency characteristics to determine the state of the flame, and the flame combustion conditions into pulse signals.
Each burner has its own specific flame shape, including its shape (envelope) and flame strength. The DPD probe thus forms a text. In the learning (Learn) mode, the frequency characteristics of the target flame signal are analyzed in real time, and the flame type (for example, flame, adjacent flame, background flame, no flame, etc.) is determined. Flame spectral characteristics image. In the "RUN" mode, the measured flame signal can be compared and identified with the archived flame to determine the state of the flame.
This digital text technology design greatly simplifies the man-machine interface and simplifies the static verification of the probe. In particular, self-diagnosis and "step-by-step" programming make the probe easy to operate.
3. Flame amplifier: Its model is DP7000, receives the flame pulse signal that the probe sends, and carries on the comprehensive processing, sends out the existence/no flame state signal, the critical flame warning signal and the 4-20mA flame signal.
Second, the installation quality of the furnace flame system of the system will directly affect the measurement results of the flame detection device, especially the detector part, which is an important part of the process of converting the flame signal into a processable digital signal. It is a primary component of the system and is Boiler furnace in front of the place. The following briefly describes several issues that the detector section should pay attention to during installation:
1. The center line of the inner frame of the detector and the flame center line of the burner should be at an angle of about 5 degrees to ensure that the detector is aligned with the initial combustion zone of the flame.
2. The detector's fiber bundle hose section should try to bypass obstructions (such as air baffles, etc.), or open holes (slots) in place on obstacles. Trial air baffles before the trial run to check whether the hose or bracket collided, taking into account the expansion of the boiler stroke.
3. Install the detector should pay attention to the direction of rotation of the furnace secondary air, the detector should be installed in the direction of rotation of the gas flow igniter 10-30 degrees.
4. The location where the detector is installed should work in the visible target area of ​​50-150cm. If the viewing area is too large or too small, it is easy to cause "peeping phenomenon" or "flame distortion".
5. Probes should be free from contamination with oil, ash, smoke, and other contaminants. The temperature of the probe mounting position must not exceed 65 °C, otherwise it will affect the life of the probe.
6. The probe must be insulated from ground. Insulation cover should be installed on the bracket. The insulating sleeve has two functions. One is to prevent heat conduction, to prevent the heat of the furnace from being conducted to the probe along the bracket, and the second is to electrically insulate to avoid interference with the measurement signal and noise. The measurement signal connection should be shielded and connected to the DCS grounding system to prevent strong electrical interference.
Third, the system's debugging and maintenance The flame system's debugging is to make the system correctly reflect the fire mouth combustion conditions, accurately identify the burning of coal or fuel, and will not peep into the upper and lower or adjacent fire mouth and the entire furnace background flame. In the debugging process, the Forney intelligent flame probe is first set statically and dynamically adjusted to adjust the flame combustion conditions. Static tuning of the probe involves configuring the probe to generate a text, then storing the text and putting it into operation. A complete text contains a set of parameters and existing flame presence/absence files. There are eight LED displays on the probe and four buttons for setting different values ​​and parameters. Three of the buttons are on the probe surface. They are Advance, Help, and Change.
Advance: Displays the file content and directory.
Help: Explain the meaning of the contents of the file.
Change: Modify the setting value in the range of the directory. Press the programming enable button before changing the number.
On the side of the probe (inside the housing) there is the Program Enable key, which is the programming enable key for programming permission.
The main steps of programming are as follows:
1. Press the Programming Enable button to set the probe in the set state.
2. Programming file text.
3. Configure the status and various parameters of the probe.
4. Adjust the angle, range and sensitivity of the probe to the flame. Learn to have a state of flame.
6. Learn the flame without state.
7. Store text data.
8. Put the probe in operation for use.
The detectors have two levels of lists, ie status lists and setpoint programming lists. The status list is only used to display the status information of the detected burner flame of the current detector. The set value list is used for static and parameter setting of the detector. Refer to Table 1 and Table 2 for the specific setting adjustment.
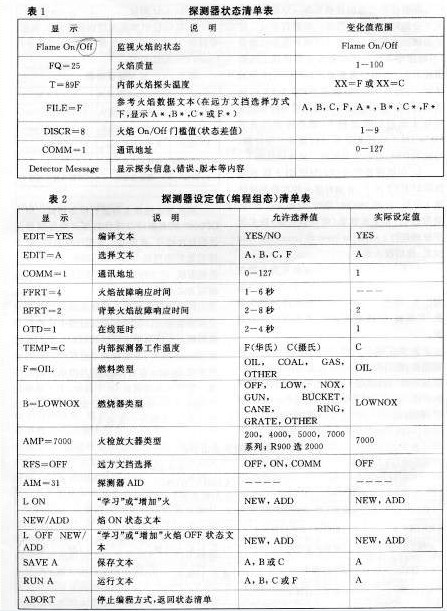
1. When the unit is under high load (above 270MW or above 90% load), the coal fire inspection is performed at the feed mill speed of 400 rev/min and 700 rpm, respectively, with the fire (burner put into operation) and without The LearnOnNew and LearnOnAdd settings are performed separately under fire conditions (burner removal) and then put into protection.
2. After the above adjustments, the unit reduced loads to 240MW (80% load) and 200MW (70% load) stable conditions, check the actual operation of the flame and perform burner injection/cutting experiments to check if it is true and whether there is any false flame.
3. In order to ensure that the fire detection can work stably under any conditions, the boiler load should be reduced to about 170 MW (without fuel injection), and then the coal fire should be checked one by one at a feed rate of 400 rpm for the LearnOnNew setting. , and then carry out LearnOnAdd adjustment at a high speed of around 700rpm.
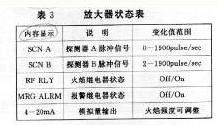
Second, configure and debug the fire detector amplifier. Each DP7000 amplifier can receive the pulse signal sent by two fire detection detectors. Xiangfan Power Plant adopts one-way configuration. The amplifier's display values ​​are also divided into two groups, the status group and the setpoint configuration group. The status group shows the operating parameters. All parameters are displayed in abbreviated form. See Table 3:
The setpoint configuration group is used to configure and modify the amplifier. In the process of dynamic debugging fire detection and determination of the relay action value according to the actual situation. We set about 200pps. In the actual debugging process, we usually have a firing frequency of about 250pps. The operating value of the sending signal relay should generally be 50 pulses lower than the measured value, and the non-fire frequency is about 150pps. The critical alarm flame action value is less than The fire action value is 20 pulses high. See Table 4
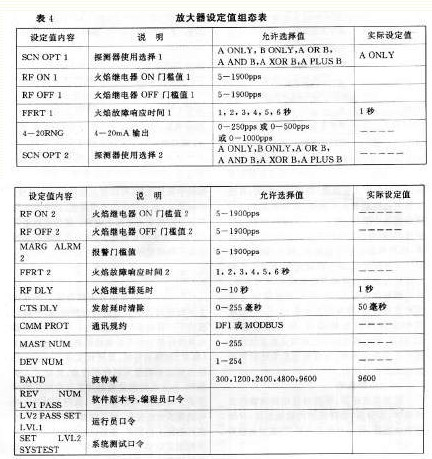
Fourth, factors that affect the flame detection and analysis of the type of boiler combustion The type of fuel on the boiler combustion equipment structure selection, boiler layout and boiler safety and economy have a greater impact, a direct impact on the boiler's combustion, and combustion status The stability and flame shape of the combustion also affect the accuracy and sensitivity of the flame detection. The following sections explain these aspects separately:
1. Effect of Burning Mode on Fire Detection Forney's fire inspection system forms a text with flame shape and flame intensity. Based on this, the text is analyzed and processed through specific software. Different combustion methods form different background flame shapes, which have different effects on the burner flame. Therefore, the processing of the flame signal in software is not universal. At the same time, the upper and lower flames or adjacent burners The influence of flame is different, and the discrimination of flame detection by digital text has a great influence.
2. The influence of combustion on the fire detection The stability of the combustion dynamic process is of great significance to the measurement of the flame. Although the stability of the combustion is directly related to the fineness of the fuel and the fuel/wind ratio, it is also closely related to the type of fuel. Inseparable. From the conventional analysis of fuels, when the coal is burned, except for a part of the fixed and free hydrogen, the elemental composition is not a single-state combustion, but a complex organic combustion is involved, and the combustion process is roughly the same as the analytical process in industrial analysis. Therefore, the factors that directly affect the combustion and operation of the boiler are mainly the industrial analysis components of coal, namely volatile matter, moisture and ash. Now briefly describe their effects on combustion:
(1) The effect of volatiles The more volatile the coal, the easier it is to ignite and the combustion is easy to complete. This is because: the volatile matter is a gas combustible material, the ignition temperature is lower, the more volatiles, the lower the ignition temperature, so that the coal is easy to catch fire; more volatile matter, relatively less than the coke fired in coal; Volatilization analysis shows that burning can release a large amount of heat, causing high temperature in the furnace, which helps the rapid ignition and combustion of coke. Therefore, the volatile coal is also more prone to burnout. The volatiles are precipitated from the solid fuel and precipitated. To make the fuel porous, the more volatiles, the greater the porosity of the fuel particles, the greater the contact surface between the fuel and air, to facilitate complete combustion. The design coal of Xiangfan Power Plant is 50% mixed for Dengfeng lean coal and Huangling bituminous coal. The flammable radical is divided into 22.62%, and the checked coal A is Henan Dengfeng lean coal with a volatile content of 14.22%. The checked coal type B is Shaanxi Huangling bituminous coal with a volatile content of 35.46%. The large-scale changes have a great influence on the detection of the fire detection system. When the coal type changes, dynamic learning adjustments are needed.
(2) The effect of moisture The amount of water in the coal is high, the effective heat released when burning is reduced, and the amount of water is high, which reduces the combustion temperature in the furnace and increases the heat of ignition. This can delay the fire and even make it difficult to catch fire.
(3) Effect of ash Not only does the ash content in the fuel not burn, but it also reduces the amount of heat generated by the fuel, hinders the correct connection between the flammable substance and oxygen, increases the difficulty of ignition and combustion of the fuel, and also increases the combustion loss. An increase in the ash content of the fuel can slow the flame propagation speed, affect the ignition, and reduce the flame temperature, because the heat consumption of the heated ash increases. The lower calorific value of coal, the greater the ash content and moisture content, the greater the temperature drop caused by the increase of ash content.
V. Conclusion Forney's intelligent flame detection system analyzes and processes the flame state through text processing, providing us with a new set of measurement methods. Based on microprocessor and software calculation and analysis, the strength (magnitude) and frequency characteristics of the flame under test are constantly inspected, and the static setting of the system and the verification of the measurement components are conveniently achieved, simplifying the man-machine operation and providing a flame detection device. The development and application have opened up new directions. However, in actual operation, changes in operating conditions or changes in coal quality have a greater impact on the accuracy and sensitivity of the measurement, and even result in erroneous results. It is necessary to continuously adjust the learning process according to the actual situation. The staff has increased the workload, and at the same time it has strict requirements on the stable working conditions in the adjustment process, and it can only be determined by raising or lowering the load several times, which increases the difficulty for the operating personnel and also increases the production and operating costs.
The truck engine consists of the following components: the body and the crankshaft linkage: cylinder block, cylinder head, piston, connecting rod, crankshaft, flywheel, and so on. Valve train: valve group, valve train, camshaft, and so on. Cooling system: water pump, water tank, fan, thermostat, etc. Lubrication system: oil pump, oil filter, oil filter, oil dipstick, and so on. Fuel system: fuel tank, gasoline pump, gasoline filter, air filter, fuel injector, etc. Ignition system: high voltage coil, distributor, spark plug, high voltage line, and so on.
Truck Engine Parts,Truck Accessories,Semi Truck Parts
Hebei Zhonghai Shipping Accessories Manufacturing Co., Ltd. , http://www.zhonghaiship.com